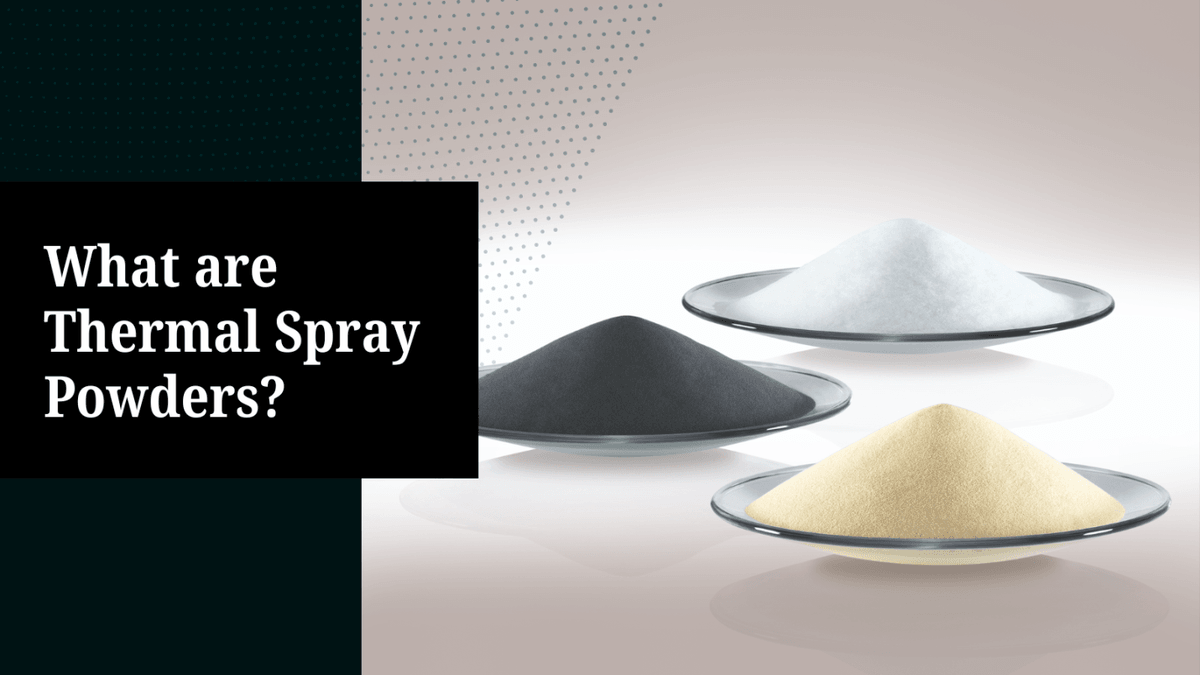
Thermal spray powders play a critical role in the thermal spray process, which is a coating technique used across various industries to enhance the surface properties of materials. This method involves the projection of molten or semi-molten materials onto a surface to create a coating that can improve wear resistance, corrosion protection, and thermal insulation.
Thermal Spray Powder Suppliers provide all types of thermal spray powders according to your requirements and the type of structure.
Understanding Thermal Spray Powders
Thermal spray powders are fine particles that serve as the feedstock material in the thermal spray process. These powders are melted or heated to a semi-molten state and then accelerated towards a substrate, where they rapidly cool and form a coating.
Types of Thermal Spray Powders
Thermal spray powders come in various compositions and particle sizes, each tailored for specific applications and coating requirements.
Here are the main types:
1. Metallic Powders
• Pure Metals: These include powders of metals like aluminium, copper, and zinc, used for applications requiring specific metal properties.
• Alloys: Alloy powders, such as stainless steel, nickel-chromium, and cobalt-chromium, offer a combination of properties like high wear resistance and corrosion protection.
2. Ceramic Powders
• Oxides: Powders like alumina, zirconia, and titania are used for coatings that require high hardness and thermal stability.
• Carbides: Tungsten carbide and chromium carbide powders provide exceptional wear resistance and are often used in harsh environments.
3. Composite Powders
These powders combine metals and ceramics to leverage the benefits of both materials, providing enhanced performance in demanding applications.
Applications of Thermal Spray Powders
Thermal spray coatings are utilized in a wide range of industries due to their ability to enhance the surface properties of components. Key applications include:
1. Aerospace
• Turbine Blades: Coatings applied to turbine blades improve resistance to high temperatures and oxidative wear.
• Landing Gear: Thermal spray coatings on landing gear components enhance wear and corrosion resistance.
2. Automotive
• Engine Components: Pistons, cylinders, and other engine parts are coated to reduce friction and wear, improving efficiency and longevity.
• Exhaust Systems: Coatings protect exhaust systems from high-temperature corrosion and wear.
3. Oil and Gas
• Drilling Equipment: Coatings enhance the wear resistance of drilling tools and components exposed to abrasive environments.
• Pipelines: Internal and external coatings on pipelines protect against corrosion and erosion.
4. Medical Devices
• Implants: Thermal spray coatings on implants, such as hip and knee replacements, improve biocompatibility and wear resistance.
• Surgical Tools: Coatings on surgical instruments enhance durability and reduce friction.
5. Power Generation
• Boilers and Heat Exchangers: Coatings protect against high-temperature corrosion and fouling.
• Wind Turbines: Components of wind turbines, such as shafts and bearings, are coated to improve wear resistance and extend service life.
Conclusion:
Thermal spray powders are essential materials in the thermal spray process, providing enhanced surface properties to components in numerous industries. Thermal spray powders offer significant benefits such as improved wear resistance, corrosion protection, thermal insulation, and overall performance.
By leveraging the advantages of thermal spray coatings, industries can achieve longer-lasting, more efficient, and cost-effective solutions for their most demanding applications. Contact Diffcor Manufacturer to understand more about thermal spray powders.